We always have turkey for Thanksgiving. I mean who doesn’t? My job wasn’t to cook it, though; it was to eat it.
How to Feed a Low-Pressure Steam Boiler
I once worked for the rep that sold McDonnell & Miller products in New York. They handed me a catalog on a Friday and told me that we would be the new rep the following Monday. I spent the weekend looking at that catalog. Not much of it made sense to me at the time, but the company had also hired a couple of the factory guys who had worked directly for M&M, so at least I had a place to ask questions, of which I had many.
This was back before there were electronic controls and the popular feeder for a low-pressure steam boiler worked with a float, similar to what’s inside a toilet tank. I learned that as the water in a boiler turned to steam it left the boiler at the very specific rate of 1/2 gallon per minute for each 1,000 square feet of equivalent direct radiation. So if a boiler had a rating of 4,000 Sq. Ft. EDR, it would lose exactly 2 GPM when the boiler was running. With the old steam boilers, this was never a problem because those old boilers contained a lot of water. But when the smaller steam boilers showed up in the ‘70s, many of them went off on low-water before the water, in the form of condensate, had a chance to return to the boiler. So satisfying a boiler’s appetite, while also trying to keep it from flooding due to too much feed water, became somewhat of a guessing game.
Later, we would have electronic feeders that knew how to wait for the condensate to return. Those modern marvels would dwell for a time and sort of look over their shoulder to see if the prodigal condensate was coming home from across the field. They were better, but nothing is perfect.
But back to those earlier float-type controls. The good folks at McDonnell & Miller pounded into my young head that contractors must use cold, not hot, water to feed their low-pressure steam boilers. This was because calcium and magnesium, the elements that are in most feed water, will come out of solution when the water gets hot. This is what causes water heaters to “kettle.” And the folks at M&M didn’t want that nasty stuff precipitating out on the seats of their mechanical water feeders because that could cause the feeders to stay open when they were supposed to be closed, and that would fill the systems with water that would overflow through the radiator air vents. Not good.
So we preached cold-water feed to all the contractors, who looked at us like we were out of our minds. How could we tell them to put cold water into a hot boiler? Wouldn’t that cause the boiler to crack due to thermal shock?
We explained that it wouldn’t because they were feeding the water into the condensate-return line, and not into the boiler itself. By the time the water reached the boiler it wouldn’t be cold anymore, so it couldn’t possibly hurt the boiler. They should look at our sincere faces and trust us.
They fed with hot water, of course. And we got a lot of calls about how “our” feeder flooded the house. Our guys would go out to see the job, and they’d tell the contractor about how hot water is bad for a mechanical water feeder, how it could foul the feeder’s seat and allow water into the system when the system didn’t need any more water. The contractors would tell our guys they were nuts.
And so it went. When the electronics showed up, a lot of those problems went away because an electronic solenoid valve closes tighter than a mechanical, float-type valve closes.
But that brings me to boiler-feed pumps. We find these on larger, low-pressure steam systems, particularly those with low-water-content boilers, and also on two-pipe steam systems that have steam traps.
A low-pressure boiler is one that never goes above 15 psig. And since the folks who make boiler-feed pumps like to have a one-size-fits-all pump, they provide one on all their stock units that that will discharge at 20 psig because high pressure goes to low pressure. Always. And to get water into a boiler that’s operating at 15-psi, you need to have at least 20-psi. It’s sort of like putting air in your car’s tires. To get in, you need more pressure than what’s already in there.
But the challenge is that most steam heating systems, and even the really big ones like the Empire State Building, are supposed to be working on a pressure not to exceed 2 psi (the Empire State Building works on 1-1/2-psi steam) So here we have this feed pump that’s capable of a Mike Tyson-like, 20-psi punch, and the boiler is operating at maybe 1 psi. Too much pressure means too much water goes into the boiler and that can cause problems.
And I’m not talking about flooding problems. The pump controller is on the boiler and it will stop the feed pump from feeding above a certain point, but the sudden inrush of relative cold water will kill the steam that’s forming in the boiler for a time.
Spriex/Sarco has some great training videos on YouTube that shows this. They boil water in a clear cylinder and make steam. Then they add a bit of feed water to the boiler. The steaming instantly stops. That can cause distribution problems on the job, so they recommend using a modulating feed pump that will dribble hot (not cold!) water into the boiler in smaller doses to keep the steaming going while the boiler is taking on much-needed water.
Feed-pump manufacturers have long talked about using a balance valve at the discharge of their pumps to eat up the excessive pressure that we don’t need to get into a boiler operating at a maximum of 2 psig. That’s the hydronic equivalent of driving a car with your right foot on the gas while your left foot’s on he brake, but it was the age-old solution until modulating pumps showed up. These are the best choice for those larger jobs.
As for the smaller jobs, I’ve found that if you feed them with the electronic feeders that are around these days you’ll have the best luck if you modulate the feed rate with a valve.
And here’s a tip for you. Feed those boilers through a small water heater. The calcium and magnesium will settle out inside the water heater instead of inside the boiler. The contactor will have to replace that small water heater as time goes by, but the boiler will last much longer, and boilers are more expensive than small water heaters.
Another tip is to add a good air separator, the sort you’d use on a hot-water heating system, to the hot-water feed line before it reaches the water feeder. That will do a nice job of removing most of the air from the hot water, which will cut down on corrosion inside the boiler and increase its life. It’s also a nice add-on to the sale, which benefits the customer, the contractor, and most important, you.
Leave a comment
Related Posts
I had written a story for Plumbing & Mechanical a while back about a fella in Canada who sent me this email: "Our problem is that five out of hundreds of univentilator co...
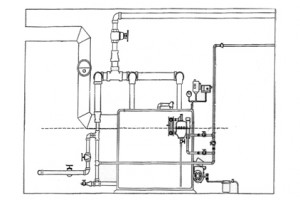
I love all the advances taking place in the world of hydronics, but I’m still seeing plenty of steam systems out there in our older cities, so knowing about dry steam wil...