This all-technical, three-hour seminar will make you familiar with the many types of old steam heating systems and what goes wrong with them. Dan Holohan’s easy-to-follow...
Sizing a Boiler for a Brewery
The most important part of the brewery steam system design is to size the boiler properly. An oversized boiler can result in frequent cycling while an undersized boiler may never be able to meet the temperature requirements of the brewery. Both of which will adversely affect the brewing process. A steam boiler should be sized according to the connected load. The connected load includes all the vessels and tanks as well as the piping. The manufacturer of the brewing equipment should provide the Btu consumption of their equipment. Another sizing consideration is the planned expansion of the brewery. Since the market is brewing and distilling market snowballing, the boiler you design today may be undersized next year. If you do an internet search, there are many rules of thumb for sizing a brewery boiler including:
50,000 Btuh per barrel of capacity,1-2 Boiler HP (BHP) per brew barrel,1 BHP per barrel for smaller brewers and 2 BHP for brewers per barrel with large hot liquor tanks. As with most rules of thumb, they may or may not be accurate for the facility. According to brew industry design expert, Blaine Clouston with Simplified Stainless, the equipment manufacturers generally ensure the heating equipment to meet the following:
Brewkettle heating - 1.5 degree F/minute
Brewkettle, evaporation - 5- 6%/hr
Mash Vessel Heating - 1.5 degree F/minute
Hot Liquor tank - ability to heat water 1.5 times the brewhouse size in 4 hours. Example; a 10 barrel system would typically use up to 15 barrels in hot liquor.
Based on his extensive engineering background, Mr. Clouston has some shortcuts which he feels are more accurate for sizing:
Brewkettle Heating and Boiling = 32,000 Btu/Hr/bbl
Hot Liquor Heating from 60-175F in 4 hours = 19,500 Btu/Hr/bbl
Mash Vessel Heating = 29,000 Btu/Hr/bbl
Bbl = Barrel
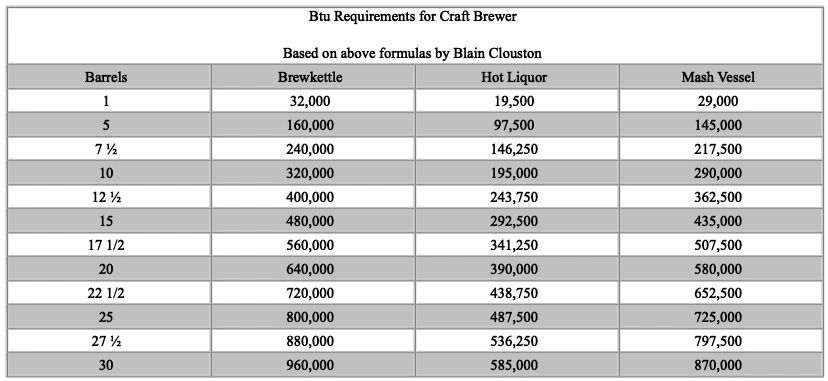
Other Brewery Boiler Sizing Options
According to the Master Brewers Association of the America's book, Brewing Engineering and Plant Operations, the following are the sizing guidelines it recommends:
50,000 Btuh per barrel of capacity.
Wort* heating prior to boiling
Btu's required to heat 1 barrel of wort from 1500F to 2120F in one hour.
1 bbl x 31 gal/bbl x 8.34 lb/Gal x (2120F -1500F) x 1 Btu/F0 = 16,030 Btu/Hr.
Wort* boiling in a kettle
Energy required to turn wort at 212 to start to boil.
1 bbl x 31 gal/bbl x 8.34 lb/Gal x 0.05 evaporation/hr x 970 Btu's/lb = 12,539 Btu/Hr.
Btu's required per barrel of Wort*
Amount of energy needed when boiling Wort in a Kettle.
Btu/Hour = 1bbl x 31 gal/bbl x 8.34 lb/ Gal x 970 Btu/ Lb
*Wort is the liquid extracted from the mashing process during the brewing of beer.
Bbl = Barrel
Additional sizing considerations
Part of the sizing calculation is whether the steam-consuming components will be operated separately or simultaneously as this affects the boiler and pipe sizing. Another item to consider is the energy required to heat all the pipes from a cold start. A rule of thumb is to add 15-30% of the processing load for the cold piping, depending on the distance the steam must travel to the process. Brewery elevation must also be factored into the design as well.
Boiler Efficiency
When your sizing is complete, you have to factor in the efficiency of the boiler as the heat load of the plant will be the output of the boiler. Most steam boilers will have an efficiency range between 80% and 85%.
For ease of calculation, let us look at the heating requirements for a 10 barrel brewery with simultaneous operation.
Brewkettle 32,000 Btuh X 10 barrels = 320,000 Btuh
Hot Liquor 19,500 Btuh X 10 barrels = 195,000 Btuh
Mash Heating 29,000 Btuh X 10 Barrels= 290,000 Btuh
SUBTOTAL = 805,000 Btuh
Cold piping loss 25% = 201,250 Btuh
Boiler Net Output = 1,006,250 Btuh
Boiler input @ 80% Boiler Efficiency = 1,257,813 Btuh
Boiler input @ 82% Boiler Efficiency = 1,227,134 Btuh
We would need a boiler with an input of about 1.2 Mil
Would you like to learn more from Ray Wohlfarth? Check out his seminars, books, and blog about brewing with steam.
Leave a comment
Related Posts
We always have turkey for Thanksgiving. I mean who doesn’t? My job wasn’t to cook it, though; it was to eat it.
I had written a story for Plumbing & Mechanical a while back about a fella in Canada who sent me this email: "Our problem is that five out of hundreds of univentilator co...