We always have turkey for Thanksgiving. I mean who doesn’t? My job wasn’t to cook it, though; it was to eat it.
What Causes Water Hammer? And How Do You Stop It?
Looking for ways to stop water hammer in your steam heating system? Here is a list of common causes for water hammer and how to prevent noisy pipes.
This is an excerpt from Dan Holohan's popular book A Pocketful of Steam Problems (with Solutions!).
The pipes don't have the right pitch.
In any steam system, the condensate is supposed to drain by gravity back to the boiler or the condensate receiver. If water lays in the pipes between firing cycles, steam will pick it up and drive it into the first available fitting. Water hammer from bad pipe pitch usually happens when the system first starts. Steam will also rapidly condense over a puddle of water causing the water to snap violently up into the partial vacuum left by the condensed steam. The proper pitch for parallel flow steam mains is one inch in 20 feet. For counterflow mains, it's one inch in ten feet.
Check the pitch with a line level.
The near-boiler piping doesn't meet the manufacturer's specs.
Nowadays, boiler manufacturers consider the near-boiler piping to be a part of the boiler. They use it to help dry the steam before it heads out toward the system. If the near-boiler piping doesn't meet the manufacturer's specs, you could be throwing water up into the piping, and this will cause water hammer.
Get the boiler manufacturer's installation-and-operating manual and check the piping on the job against their drawings in their booklet.
The steam quality is bad.
The quality of the steam greatly affects water hammer. It's not just faulty near-boiler piping that can throw water up into the system. Dirty water, or water that has a too-high pH high can do it as well. This type of water hammer usually happens during the middle of the firing cycle. Look closely at the boiler's gauge glass. If the steam is dry, the part of the gauge glass above the water line should be dry as well. Try raising the water line to within an inch of the top of the gauge glass. If the water in the boiler is clean, it will not surge over the top of the gauge glass.
Check the pH of the water with pH paper. A good pH for a steam system ranges between seven and nine. If the pH gets to 11, the water will start to prime and foam and carry over into the system, causing water hammer. Dead Men often added vinegar to steam heating systems to lower the pH and lessen the priming and surging.
Make sure the piping is right, and that the water is clean.
The boiler is overfired.
If you overfire a boiler, the water will surge violently and some water will carry over into the pipes. This type of water hammer usually happens during the middle of the firing cycle. You should fire to the connected load of the boiler (piping and radiation). This is the boiler's D.O.E. Heating Capacity load.
Don't oversize replacement boilers. Always check the firing rate against the connected load.
The steam pipes aren't insulated at all.
You're supposed to insulate the supply pipes in a steam system so the steam doesn't condense on its way to the radiators. Bare pipes lose five times as much heat as insulated pipes. Without insulation, the piping's ability to condense steam may exceed the boiler's ability to produce steam. You'll often wind up with radiators at the ends of the main that won't heat well. But worse than that, you'll wind up with water hammer when the system first starts. The cold, uninsulated pipes create more condensate than they can handle. When the steam hits all that water, you get water hammer.
Insulate the steam lines.
The boiler's water line is priming or surging.
Dirt is usually the culprit here. When you see droplets of water in the part of the gauge glass above the water line, it's time to clean the boiler. If the boiler is priming and surging, it's also probably throwing water up into the piping, and that can cause water hammer.
Try raising the water line to within an inch of the top of the gauge glass. If the water in the boiler is clean, it will not surge over the top of the gauge glass. If it does, clean the boiler and the system piping.
There's a long nipple on the Hartford Loop.
There should be either a close nipple or a wye fitting at the point where the equalizer and the wet return join to form the Hartford Loop. If you use a long nipple between the boiler's equalizer and the wet return, the returning water will surge forward violently as steam bubbles condense in the equalizer. A close nipple or wye fitting will lessen the distance the returning condensate has to travel and cure the water hammer. This type of water hammer usually happens near the end of the firing cycle.
Check this critical point in your gravity-return systems, and make sure it has either a close nipple or a wye fitting.
The Hartford Loop's close nipple or wye fitting is too close to the boiler's water line.
Check to see if the water level in the boiler can drop to a point where steam gains access to the wet return through the boiler's equalizer. If it can, the steam will quickly push down into the wet return and create water hammer. This usually happens toward the end of the cycle.
Check the boiler manufacturer's specifications on the proper level for the close nipple or wye fitting. If it's too high, lower it to the proper level.
The system was flooded.
Steam pipes are supposed to carry air, steam and a little bit of water. If someone left a feed valve open and the pipes filled with water, there's a good chance all the pipes have sagged on their hangers. This is a sure cause of water hammer. You'll hear it when the system first starts.
Flooding also causes sludge to wash down from the radiators. This sludge can lodge in the horizontal runouts to the risers and cause water hammer in the middle of the cycle. It will also make it difficult to deliver steam to the upper radiators.
There's a telltale sign that there's sludge in the riser: The radiator vents will "pant." Remove the vent and hold a lit match next to the hole. Watch the flame. As the radiator "pants," the flame will tilt toward and away from the hole. This happens because steam is quickly condensing in a pocket of trapped water near the base of the riser.
You may have to disconnect the riser and flush the lines to cure this one. Also, make sure you check the pitch of the mains with a line level.
The mains aren't properly dripped.
If enough water hangs around in the mains too long it's bound to run into steam and that's when the water hammer begins. To get rid of the water, you have to drip the mains. In mains where the steam and condensate travel in the same direction, there should be a drip line every 150 feet. If the steam and the condensate flow in opposite directions you need a drip every 50 feet.
If you have a one-pipe steam riser that feeds up more than one floor you should ideally drip it into a wet return or into a dry return through a loop seal or a steam trap. Dripping two-pipe steam risers isn't as critical because the condensate returns through a separate line. Just keep in mind that any steam pipe will be more efficient if you drip it.
To avoid water hammer, always keep the steam and the condensate as far away from each other as you can. Look around for places where water can gather and drip it.
The gravity-return line is clogged.
It's going to happen eventually because a steam heating system is open to the atmosphere. The pipes corrode, and sludge, rust and sediment washes down into the gravity wet-return line where the condensate moves very slowly. As the return line clogs, the condensate has a tough time flowing out of the main and into the wet return. If water lays in the main, it will meet steam, and that's when the hammering begins. This usually happens at the far ends of the mains and almost always in the middle of the firing cycle. Water will also squirt from your end-of-main vents.
You can usually flush the returns to get rid of the sludge, but there will be times when it will be easier to replace those returns. Do one or the other.
The system has motorized valves.
If it's a gravity-return system, and there are motorized valves on the supply lines, water will back out of the boiler when a valve closes against steam pressure. Adding a check valve to the return doesn't help much. Sure, it will keep the water from backing out of the boiler, but the steam pressure in the boiler will quickly overcome the lack of steam pressure downstream of the closed motorized valve. Condensate won't drain from the mains, and water hammer will follow.
Motorized valves really have no business being on a gravity-return system. You may have to add a boiler-feed pump and steam traps to cure this one. Always avoid using motorized valves on gravity-return systems.
The radiators aren't pitched properly.
A one-pipe steam radiator has to pitch back toward its supply valve so the condensate can flow out of the radiator. If you let the condensate build up inside the radiator, you'll have water hammer and squirting radiator air vents. Use a bubble level to check the pitch.
When you're dealing with a large radiator, check the pitch from section to section. Big radiators often sag in the middle, and a long level might not pick this up. Don't go by eye because your eyes can play tricks on you.
Use small blocks of wood or plastic checkers to prop the end of the radiator up. Notice, too, how an old radiator will dig a trench into a wooden floor. That comes from years of expansion and contraction. Don't go by eye when you're checking the pitch. Always use a level.
It's one-pipe steam, and the supply valves aren't fully opened.
If they're not, you'll get water hammer as steam and condensate try to pass each other in that tight space. The valve on a one-pipe-steam radiator is a service valve. It has to be either fully opened or fully closed. Anything between will cause water hammer problems.
If you think the valve is fully opened and you're still getting water hammer, check to make sure parts of the valve haven't fallen off and lodged in the valve's seat.
If the valve is new, check its internal size. Steam supply valves of the old days had more space inside than their modern replacements. You may have to use a bigger size.
The steam traps aren't working.
A two-pipe-steam system is like a ladder. Each radiator is a rung on that ladder, and at the end of each rung you'll find a steam trap. Part of the trap's job is to keep steam from entering the no-pressure side of the "ladder." If even one trap fails in the open position, steam will jump across and hammer into the water that's trying to drain from the other radiators. This water hammer will damage the working steam traps, and that will make the problem even worse.
At the ends of mains and at the base of risers, float & thermostatic and bucket traps serve the same purpose as radiator traps. If they fail in the open position, or, with bucket traps, if they lose their prime water, steam will move into the dry return lines and cause water hammer. Trap maintenance is essential. Don't neglect it.
The radiator air vents are too quick.
Quick vents let the air race out of a radiator, but they also let the steam race in. When you quickly heat a large radiator, you're going to get a lot of condensate. That heavy load of condensate can't drain easily against the steam that's rushing through the supply valve. The result is water hammer and a squirting air vent.
If you suspect this is your problem, try an air vent with a slower venting rate. This simple trick often works wonders when it comes to water hammer. Not every radiator needs a quick vent.
In replacing the boiler, someone tuned a wet return into a dry return.
If you have a gravity-return system the lowest, horizontal, steam-carrying pipe has to be a minimum distance above the boiler. In one-pipe steam, that distance is 28 inches. In two-pipe, gravity-return steam, you need a minimum of 30 inches for every pound of pressure in the boiler. So, for instance, if you operate the boiler at two psi, you need 60 inches. If you operate the boiler at three psi, you need 90 inches. The Dead Men knew this, and they piped their wet and dry returns accordingly. A new boiler with a low water line just might turn a wet return into a dry return. If it does, you'll have some very memorable water hammer in the middle of the firing cycle.
Measure the distance between the boiler's water line and the lowest steam-carrying pipe. And take your time looking around the basement because that pipe could be anywhere.
There's a concentric reducer in the steam main.
A concentric reducer will allow condensate to collect if the condensate flows from a large pipe to a small pipe. That causes water hammer at the start of the cycle.
Use an eccentric reducer, or drip the main just before it enters the concentric reducer.
There's not enough vertical space between the boiler water line and the end of the main.
We commonly call this space the "A" Dimension. You need 28 inches of "A" Dimension on a gravity-return, one-pipe steam system. Returning condensate stacks in that space and builds pressure. That pressure combines with the "leftover" steam pressure at the end of the main to put the condensate back into the boiler. If the job doesn't have enough "A" Dimension, water will back into the main and cause water hammer in the middle of the cycle.
This often happens when an installer removes a boiler from a pit and replaces it with a new boiler that's not in the pit. The higher water line of new boiler shortens the "A" Dimension and causes the water hammer.
Either lower the boiler, or use a condensate- or boiler-feed pump.
The Hartford Loop isn't piped properly.
Make sure the connection between the return and the equalizer is far enough below the boiler's water line. If steam can work it's way down the equalizer and into the wet return it will hammer, and usually at the end of the cycle.
See if there's a long nipple on the Hartford Loop. Long nipples create water hammer as the condensate returns. Replace the long nipple with either a close nipple or a wye fitting.
The condensate- or boiler-feed pump discharges into a Hartford Loop.
The Hartford Loop does a good job of protecting the boiler in a gravity-return system. Should a return line spring a leak, water can flow from the wet returns, but because of the Loop, it can't flow from the boiler.
On a gravity-return system, the wet return connects to the boiler's equalizer at a point about two inches below the lowest operating point. This varies from manufacturer to manufacturer so you should always check their installation instructions.
When you have a condensate pump, you no longer have a gravity-return system. Should a return spring a leak, the boiler water can't back out of the boiler because of the condensate pump's check valve. Should the check valve fail, boiler water will back into the condensate pump. The pump will turn on and pump the water back into the boiler. Should the check valve and condensate pump fail simultaneously, water will back into the pump's receiver and rise up the vent piping. Since this piping is usually several feet higher than the boiler's water level, the water still can't get out.
If there's an overflow pipe in the vent line, however, the condensate can back out of the boiler, should both the pump and check valve fail. In this case, a Hartford Loop would help on a pumped return system. But other than that, the Loop may cause problems. Water under pressure from the pump can splash up into the boiler header and create water hammer. If this is your problem, relocate the pump's discharge line to the bottom of the boiler's equalizer.
Leave a comment
Related Posts
I had written a story for Plumbing & Mechanical a while back about a fella in Canada who sent me this email: "Our problem is that five out of hundreds of univentilator co...
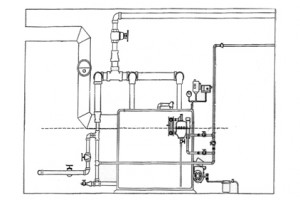
I love all the advances taking place in the world of hydronics, but I’m still seeing plenty of steam systems out there in our older cities, so knowing about dry steam wil...